The Economics of Aerospace CNC Machining
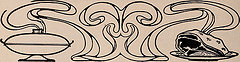
Cheap overseas manufacturing has long asked searching questions of the UK manufacturing industry which has struggled to compete on price. The economics of CNC machining has pushed us towards an emphasis on specialist precision CNC machining like the manufacture of aircraft gears, Gleason System bevel gears, tight meshing involute splines and gear hobbing to international standards.
Feasibility Study
It is normal for a company to embark on a feasibility study prior to the purchase of any capital equipment such as a CNC machine tool. This study fulfils many functions, such as determining the capacity and power required together with its configuration – horizontal/vertical spindle for a machining centre, or flat, or slant bed for a turning centre. Many other features must also be detailed in the study, encompassing such factors, in the age of 5-axis machining, as the number of axes required and whether the machine tool should be loaded manually, by robot, or using pallets. An exhaustive list is drawn up of all the relevant points to be noted and others that at first glance seem rather esoteric, but will affect the ability of the company to manufacture its products. It has been shown time and again that many mistakes have been made in the past when companies rush into the purchase of new equipment without considering all of the problems, not only of the machine tool itself, but of the manning and training requirements together with its effect on the rest of the machine shops productive capability. Often the fact that an advanced, highly
productive machine is now present in the shop could affect the harmonious flow of production, causing bottlenecks later, when the purpose of purchasing the machine was to overcome those problems at an earlier production stage. Aerospace machine tools have even been purchased in the past without due regard for the components they must manufacture, or without correct assessment of future work.
This latter point is not often considered, as many companies are all too concerned with today’s production problems rather than those of the future. Taking this theme a little further, in a volatile market a feasibility study should perceive not only the short and medium term productivity goals, but also the long term ones, as it is often the long term trends of productive capability which are the most important if a company is tc amortise their costs. When highly sophisticated plant such as an FMS is required, it can be several years from its original conception before this is a reality on the shop floor, and a company’s production demands
may have changed considerably in the meantime. If, for any reason, the wrong machine has been purchased, or more likely, something has been overlooked during the feasibility study, then the “knock-on effect” of this poor judgement is that it will have cost the company dearly and, at the very least, any future study will be looked on by the upper management with disdain and scepticism.
A company should plan and discuss their products and systems to be implemented in the future with an eye on the production equipment of the present. This is relevant, as any responsible production engineering company will invest in manufacturing equipment which has reached a reliable level of maturity, yet at the same time allow for further growth over a foreseeable time, and in such a manner, maintain and strengthen the competitiveness of the enterprise. Sophisticated technologies – although they create conditions for optimum utilisation of the plant – mean that capital equipment is more costly to purchase. Whenever high cost equipment is purchased it is usually the intention of a company to maximise their financial outlay by reducing the pay-back period to a minimum, using second and possibly a third shift. This strategy has the effect of lowering the hourly machine rate drastically, or to put it another way, these systems are over-compensated by more intensive utilisation, so that despite the higher amount invested, a better utilisation and in most cases higher machine performance will achieve a reduction in costs.
It is precisely in this area that the largest amount of manoeuvring space for entrepreneurial decisions occurs. In the early 1980s, a review regarding machine tool utilisation was conducted and the results showed that on average only approximately 700-800 hours per annum were spent actually doing “cutting” work. If one refers this to the theoretically available annual loading time for the machine tool of 364 x 24 hours per day, this time will represent approximately 8%. Obviously, improvements during the last 20 years in the cutting capability of machine tools and their performance have shown increases averaging
500% and further drastic savings of time have been achieved in the area of idle times – where higher rapid traverse rates and automatic tool and workpiece-changing equipment have been developed. It nevertheless remains a fact, that even though these are impressive productivity gains, they are a “drop in the ocean” when seen from the overall view of the plant utilisation throughout the year.
So much for the likely problems that face a company embarked on a feasibility study for the purchase of new equipment. Just what are the advantages to be gained from the purchase of the “correct” plant? One of the main purposes in using a CNC machine tool is to increase the productive throughput with this equipment. Although high volume production can occur using CNC equipment, it is not alone in this area and under certain conditions can be surpassed by using more conventional technologies, such as, single and multi-spindle lathes, or plug board machine tools. The major feature of a CNC machine tool is its ability to cut down drastically the lead times for similar components manufactured by a different plant. Even complex doublecurvature component geometries can be quickly and successfully programmed by a trained employee using on- or off-line programming methods. The real advance in machine tool design and monitoring systems has meant that accuracy and repeatability of a component’s dimensional characteristics can be confidently predicted, thus time and again uniform work results.
This repeatability has the added bonus of reducing inspection, assembly and fitting costs by the virtual elimination of re-work and scrap. Storage of the part program and its retrieval also has the effect of decreasing the lead times over the more conventional manufacturing methods still further. As a consequence of this feature, the skill level is retained by the company and does not leave when the employee moves on, or retires. Other indirect, but crucial advantages accrue through the application of CNC technology and include: the precise processing of changes to the part with the minimum of disruption of production, improved planning and scheduling results, repeat orders are easily undertaken, plus many more attractive benefits. The results of these improvements of reduced tooling requirements and inventories together with the administration benefits can be summarised graphically by the simple profit and loss statement against time. Any machine tool is only making money when it is cutting material and it is important to maximise this fact by improving the machine’s utilisation over second/third shifts and by other non-productive machining time advances.
Positive advantages occur when a company embraces the current CNC machining technology, but only, hopefully, after an exhaustive feasibility study.
Aviation-database.com has lots of resources for the aircraft industry. The web is a vast source of information. Aviation-database collects the industry into one huge database of contacts. Tradex Instruments Ltd with clients including Goodrich Aerospace, Muirhead Aerospace and BAE Systems is featured as a company that has successfully wrestled with the economics of aerospace CNC machining.